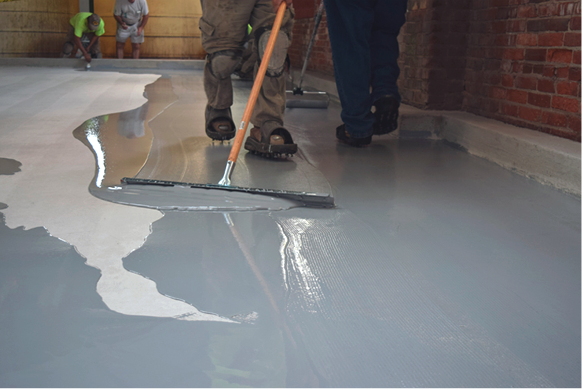
Moisture in cement can lead to a host of problems, including weakening of the structure, mold growth, and damage to finishes. Whether it’s a newly poured concrete slab or an existing surface affected by moisture, knowing how to effectively pull moisture out of cement is essential for maintaining the integrity and durability of the material. In this article, we explore various methods and techniques for removing moisture from cement surfaces to ensure long-lasting performance and aesthetics.
Absorption Techniques
Desiccants and Absorbent Materials
Desiccants and absorbent materials such as silica gel, activated charcoal, or clay absorb moisture from the surrounding environment, making them effective tools for pulling moisture out of cement. These materials can be placed directly on the affected surface or enclosed in containers to create a moisture-absorbing environment. By absorbing excess moisture, desiccants help accelerate the drying process and prevent moisture-related issues such as efflorescence and mold growth.
Vapor Barrier Installation
Installing a vapor barrier beneath or on top of the cement surface helps prevent moisture from migrating into the concrete substrate. Vapor barriers can be made of plastic sheeting, waterproof membranes, or specialized coatings that create a barrier to moisture penetration. Proper installation and sealing of vapor barriers are essential to ensure effective moisture protection and long-term durability of the cement structure.
Hygroscopic Additives
Hygroscopic additives such as calcium chloride or lithium-based compounds chemically absorb moisture from the air, reducing humidity levels and accelerating the drying of cement surfaces. These additives are often mixed into the concrete mix or applied as surface treatments to promote moisture removal and prevent moisture-related issues such as cracking and spalling. By incorporating hygroscopic additives into cement formulations, builders can enhance the drying process and improve the overall performance of concrete structures.
Mechanical Drying Methods
Dehumidification Systems
Dehumidification systems remove moisture from the air through condensation and drainage, creating a dry and controlled environment conducive to moisture removal from cement surfaces. Portable or stationary dehumidifiers can be placed in enclosed spaces such as basements, crawl spaces, or construction sites to reduce humidity levels and accelerate the drying process. By maintaining optimal humidity levels, dehumidification systems help prevent moisture-related problems and ensure the quality and durability of cement structures.
Air Circulation and Ventilation
Promoting air circulation and ventilation is essential for facilitating moisture evaporation and drying of cement surfaces. Opening windows, using fans, or installing ventilation systems help create airflow and exchange indoor air with drier outdoor air, speeding up the drying process. Proper ventilation also helps prevent condensation buildup and mold growth, improving indoor air quality and maintaining a healthy environment. By maximizing air circulation and ventilation, builders can effectively pull moisture out of cement surfaces and reduce the risk of moisture-related damage.
Heat Application
Applying heat to cement surfaces accelerates the evaporation of moisture and promotes faster drying. Heating methods such as infrared heaters, radiant heat systems, or portable heaters can be used to warm the surface temperature of concrete slabs, floors, or walls, facilitating moisture removal and reducing drying time. Care must be taken to avoid overheating or thermal stress that may cause cracking or other damage to the cement structure. By applying controlled heat to the affected area, builders can expedite the drying process and ensure the successful removal of moisture from cement surfaces.
Chemical Treatments
Calcium Chloride Testing
Calcium chloride testing is a standard method for measuring moisture vapor emission rates from concrete surfaces. By placing calcium chloride test kits on the concrete surface and measuring the weight gain over a specified period, builders can assess the rate of moisture evaporation and determine the need for moisture mitigation measures. Accurate moisture testing helps identify areas of concern and guide the selection of appropriate chemical treatments to address moisture-related issues effectively.
Liquid Sealants and Waterproofing Compounds
Liquid sealants and waterproofing compounds create a protective barrier on the surface of cement structures, preventing moisture intrusion and enhancing moisture resistance. These products can be applied as coatings, sealers, or penetrants to seal pores, cracks, and other vulnerable areas in the cement substrate. Waterproofing compounds may contain polymers, resins, or silicates that form a durable and waterproof membrane, preventing water penetration and reducing the risk of moisture-related damage such as spalling or staining.
Moisture Mitigation Systems
Moisture mitigation systems such as epoxy moisture barriers or moisture-blocking primers are designed to prevent moisture migration from the concrete substrate to the surface finish. These systems penetrate into the concrete pores, forming a moisture-resistant barrier that blocks moisture vapor transmission and protects against moisture-related issues such as adhesive failure or flooring damage. By installing moisture mitigation systems, builders can effectively manage moisture levels and ensure the long-term performance and durability of cement surfaces.
Time and Patience
Allowing Natural Drying Time
One of the most straightforward methods for pulling moisture out of cement is to allow natural drying time. Depending on environmental conditions such as temperature, humidity, and airflow, cement surfaces will gradually dry over time as moisture evaporates into the surrounding air. Patience is essential when allowing concrete to dry naturally, as rushing the process may lead to premature finishing or moisture-related problems such as cracking or surface defects.
Monitoring Moisture Levels
Monitoring moisture levels in cement surfaces is critical for assessing drying progress and determining when additional drying measures are needed. Moisture meters, hygrometers, or relative humidity sensors can be used to measure moisture content and humidity levels in concrete substrates. Regular monitoring allows builders to track changes in moisture levels over time, identify areas of concern, and adjust drying strategies accordingly to ensure optimal drying conditions and prevent moisture-related issues.
Patience in the Remediation Process
Remediating moisture-related issues in cement structures requires patience and persistence to achieve long-lasting results. Whether it’s addressing moisture intrusion, repairing damage, or implementing preventive measures, remediation efforts take time to yield effective outcomes. By adopting a patient and systematic approach to moisture remediation, builders can identify underlying causes, implement appropriate solutions, and restore the integrity and performance of cement surfaces for years to come.
In conclusion, effectively pulling moisture out of cement is essential for maintaining the integrity, durability, and aesthetics of concrete structures. By understanding the causes and consequences of moisture in cement, employing appropriate drying methods and techniques, and exercising patience and diligence throughout the remediation process, builders can ensure the successful removal of moisture and the long-term performance of cement surfaces. Whether it’s absorption techniques, mechanical drying methods, chemical treatments, or a combination of approaches, there are various strategies available to pull moisture out of cement and protect against moisture-related issues.